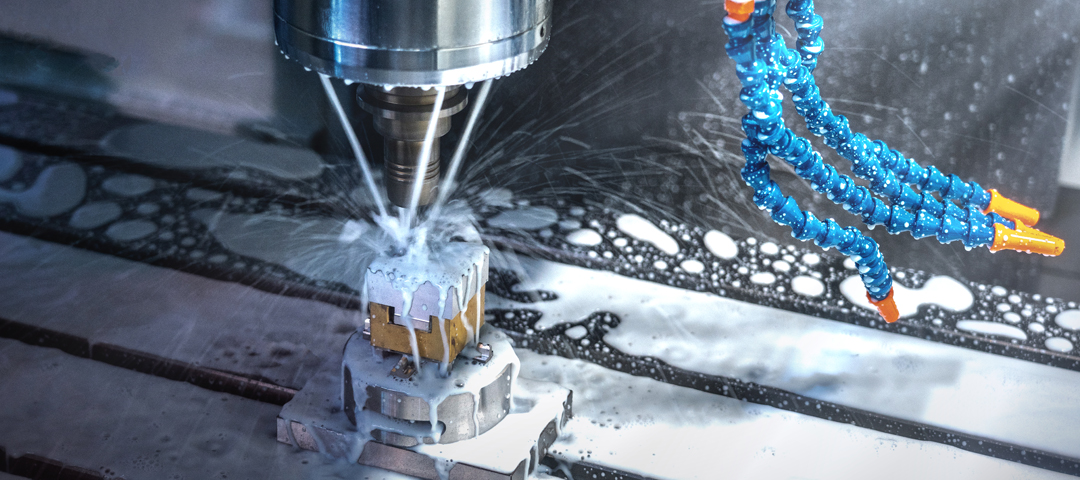
Application of CNC machining parts in the electronics industry
The Key Role of CNC in the Production of Complex Circuit Board Design
Complex circuit boards typically contain small details such as circuits, solder pads, and component mounting holes. CNC machining provides high-precision cutting, drilling, and milling to ensure the accuracy and precision of circuit boards. Helps ensure Signal integrity and stability of the circuit board. Complex circuit boards are often multi-layer structures, with each layer having specific circuits and components. CNC machining achieves precise stacking, drilling, and milling of multiple layers of boards, ensuring accurate alignment and connection between different layers.
CNC machining has a high degree of automation and precise control capabilities, completing the production of complex circuit boards in a relatively short time. Compared with traditional manual processing, CNC processing can improve production efficiency and productivity, and reduce the possibility of Human error.
CNC machining quickly adjusts and modifies the machining program according to design requirements to meet the customized needs of different complex circuit boards. Support rapid prototyping and low volume production. The CNC machine tool is equipped with an automated detection and correction system, which monitors errors in the processing process in real-time and automatically corrects them.
Key points of precision drilling and milling of electronic components
Precision drilling and milling of electronic components usually refers to the use of CNC machining technology for high-precision and high-efficiency drilling and milling operations. This processing process is applied to the manufacturing of electronic components such as substrates, heat sinks, connectors, and other components.
The manufacturing of electronic components usually requires drilling holes to install component pins, circuit connections, or heat dissipation holes. CNC drilling machines accurately control the drilling depth, diameter, and position, achieving highly accurate drilling operations. Drilling operations are adapted to different materials and requirements through appropriate tools and cutting parameters.
In the manufacturing of electronic components, milling operations are commonly used to manufacture complex shaped components, such as heat sinks or shells. CNC milling machines can precisely remove materials and create the desired shape and size by controlling tool movement and cutting parameters. Milling operations can use different types of tools, such as flat milling cutters, ball end milling cutters, and end milling cutters. In the process of precision drilling and milling of electronic components, common materials include metals (such as aluminum, copper, stainless steel) and plastics (such as polyimide, polyurethane, PVC). The processing characteristics of different materials are different, so it is necessary to choose appropriate cutting tools and processing parameters based on the hardness, thermal conductivity, and corrosion resistance of the materials.
In the process of precision drilling and milling of electronic components, Computer-aided design (CAD) and Computer-aided manufacturing (CAM) software are usually used to design and generate machining programs. CAD software is used to create or import 3D models of components, while CAM software is used to convert the models into machining instructions that can be recognized by the machine tool. Quality control is crucial in the precision drilling and milling process of electronic components. By using the automated inspection system, measurement tools, and quality control process of the machining center, ensure that the processed components meet the specifications and requirements.
Steps and advantages of CNC machining customized connectors and sockets
Design and modeling: use Computer-aided design (CAD) software to create 3D models of connectors and sockets. Customize according to specific requirements, including shape, size, hole location, pin layout, etc.
Manufacturing program
use Computer-aided manufacturing (CAM) software to convert the designed model into processing instructions that can be recognized by CNC machine tools. CAM software generates machining paths and cutting parameters according to design requirements, ensuring accurate and efficient machining processes.
Material selection: Select appropriate materials for processing according to the application requirements of connectors and sockets. Common materials include metals (such as copper, aluminum, stainless steel) and plastics (such as polyimide, polyurethane, PVC). Different materials have different conductivity, heat resistance, and corrosion resistance, so they need to be selected according to specific needs.
CNC machining operations
Use CNC machine tools for machining operations, including milling, drilling, cutting, and thread processing. CNC machine tools have high-precision positioning and control capabilities, enabling the processing of complex shapes and precise dimensions. By using different types of cutting tools and process parameters, various requirements for connectors and sockets can be met.
Quality control
Quality control is crucial during the processing process. Use automated testing systems, measurement tools, and quality control processes to ensure that processed connectors and sockets meet specifications and requirements. Quality control also includes checking the connection performance, electrical performance, and durability of connectors and sockets.
By using CNC machining technology to create custom connectors and sockets, providing high precision, efficiency, and flexibility.
Ensure strict tolerances for electronic parts during CNC machining
First, we need to use Computer-aided design (CAD) software to create accurate 3D models. Ensuring the accuracy of the model is the first step in ensuring tolerance. Select the applicable CNC machine tool according to the requirements of electronic components. Different machine tools may have different accuracy and capabilities, and choosing the appropriate machine tool can better control tolerances.
In the CNC machining process, it is necessary to carefully plan the parameter settings of each process, including tool selection, cutting speed, feed speed, etc. Minimize tolerance by optimizing process parameters. After CNC machining is completed, high-precision measuring tools such as micrometers and coordinate measuring machines are used to measure electronic components.
CNC machine tools need to be calibrated regularly to ensure their accuracy and stability. The accuracy of machine tools is crucial for maintaining the stability of tolerances. Strict quality control is carried out throughout the entire CNC machining process. This includes inspection and verification of raw materials, tools, and process parameters to ensure that the product meets specifications.
Continuously improve the CNC machining process by collecting and analyzing production data. Assist in identifying potential issues and taking corrective measures to further improve tolerance control.
How CNC Automation Simplifies Electronic Production Lines
Using CNC machine tools for automated processing to achieve high-precision and high-efficiency electronic component manufacturing. Compared to traditional manual operations, CNC automated processing can provide faster processing speed and more stable quality.
In addition to machining, CNC automation is applied to the automated assembly of electronic components. By using robots and automation systems, automatic picking, positioning, and assembly of parts can be achieved. Improve assembly speed and accuracy, reduce manpower requirements and assembly errors.
CNC automation is applied to the quality control process of electronic products. Automated quality inspection of electronic products is carried out through the use of sensors, visual systems, and automatic detection equipment. Improve product consistency and quality, and promptly identify and correct potential issues.
CNC automation combines information technology to achieve automated management and monitoring of production data. By using real-time data collection and remote monitoring systems, the operational status, production efficiency, and quality indicators of the production line are monitored and analyzed in real-time.
CNC automation provides flexibility and customization capabilities for production lines. By using programmable control systems, quickly adjust the parameters and processes of the production line to meet the needs of different products.
CNC for rapid prototyping of electronic devices
First, use Computer-aided design (CAD) software to create a three-dimensional model of electronic equipment. This includes circuit board design, shell design, and the design of various components. Ensuring the accuracy of the model is the key to ensuring the success of prototype production.
Based on the designed CAD model, write the control program for CNC machine tools. These programs guide the motion and cutting operations of CNC machine tools to achieve the designed shapes and dimensions. According to the requirements of the prototype, prepare suitable materials such as circuit board materials, metal sheets, plastic materials, etc. Ensure the quality and adaptability of materials to meet the needs of prototype production.
Use CNC machine tools for prototype machining. According to the control program, CNC machine tools will automatically perform cutting, milling, drilling and other operations to process materials into the shape and size required for design. CNC machining provides high precision and repeatability, which can ensure the quality and accuracy of the prototype.
After completing CNC machining, assemble each component. For example, welding of circuit boards, assembly of components, etc. After assembly, perform functional and performance tests on the prototype to verify the correctness and feasibility of the design. Make necessary improvements and adjustments based on the testing results and feedback of the prototype. Involving design modifications, material replacement, or process adjustments. Through continuous iteration and improvement, gradually optimize the prototype to bring it closer to the requirements of the final product.
The use of CNC for rapid prototyping of electronic devices greatly shortens the manufacturing cycle, improves the accuracy and reliability of prototype production. Assist designers in quickly validating design concepts, conducting functional testing and market evaluation, thereby accelerating the product development process.
CNC has significant cost-effectiveness in electronic component manufacturing
CNC automation reduces the need for manual operations and reduces labor costs. Compared to traditional manual operations, CNC machine tools can achieve automated processing and assembly, thereby reducing labor investment. CNC machining achieves high-speed and high-precision processing in electronic component manufacturing. Compared to traditional machining methods, CNC machine tools can process at a faster speed and maintain a higher level of consistency and quality.
CNC automation provides higher machining accuracy and stability, reducing errors and scrap rates in the manufacturing process. Compared to manual operation, CNC machine tools can more accurately control processing parameters, avoiding manufacturing defects caused by human factors.
CNC processing is quickly adjusted and customized according to different product requirements. By modifying the control program, different products can be processed in a short period of time. CNC machining saves material costs by optimizing cutting paths and minimizing material waste.