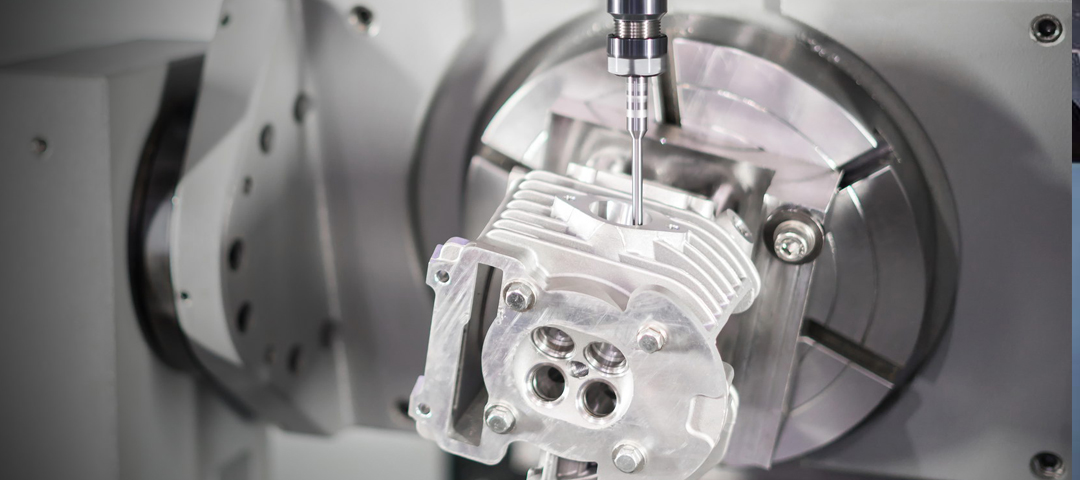
CNC plastic processing ,Types of CNC machining operations
CNC plastic processing
CNC plastic processing is the process of using CNC machine tools to process plastic materials. Compared with traditional manual or semi-automatic processing methods, CNC plastic processing has higher accuracy, efficiency, and consistency.
High precision: CNC machine tools can achieve high-precision processing of plastic materials through computer control. By controlling precise tool paths and machining parameters, sub millimeter level machining accuracy can be achieved.
Complex shape processing: CNC plastic processing can achieve the processing of complex shaped plastic parts. Through CNC programming, the motion path of the cutting tool can be accurately controlled, thereby achieving the machining of complex geometric shapes, holes, grooves, and surfaces.
Automation and efficiency: CNC machine tools automatically complete the machining process through computer control, without the need for manual intervention. This improves production efficiency, reduces labor costs, and achieves high consistency and repeatability in mass production.
Flexibility and rapid change: By modifying the CNC program, it is possible to quickly process plastic parts of different models or designs. Compared to traditional manual or semi-automatic processing methods, CNC plastic processing has higher flexibility and can adapt to different production needs.
Material saving: CNC plastic processing can effectively utilize plastic materials and reduce waste generation. Minimize material waste by optimizing tool paths and processing strategies.
Quality control: In the process of CNC plastic processing, the processing parameters and motion paths are controlled by computers, which can achieve strict quality control. Through real-time monitoring and feedback, processing parameters can be adjusted in a timely manner to ensure the accuracy and quality of plastic parts.
CNC plastic processing is widely used in plastic product manufacturing, electronic equipment, automotive parts, medical devices, and other fields. It provides an efficient, accurate, and repeatable processing method that helps improve production efficiency, reduce costs, and meet the high-quality requirements for plastic parts.
CNC machining tolerance table
CNC turning
The cutting process in which the workpiece rotates and the turning tool moves in a straight or curved line within a plane. Turning is generally carried out on a lathe to process the inner and outer cylindrical surfaces, end faces, conical surfaces, forming surfaces, and threads of workpieces.
The machining accuracy of turning is generally IT8~IT7, and the surface roughness is 1.6~0.8 μ M.
1) Rough turning aims to improve turning efficiency by using large cutting depths and large feed rates without reducing cutting speed, but the machining accuracy can only reach IT11 and the surface roughness is R α 20-10 μ M.
2) Semi precision and precision turning should adopt high-speed and small feed rates and cutting depths as much as possible, with machining accuracy of IT10~IT7 and surface roughness of R α 10~0.16 μ M.
3) Using finely polished diamond turning tools on high-precision lathes for high-speed precision turning of non-ferrous metal parts can achieve machining accuracy of IT7~IT5, and surface roughness of R α 0.04-0.01 μ m. This type of turning is called "mirror turning".
CNC milling
Milling refers to the use of rotating multi blade cutting tools to cut workpieces, which is an efficient machining method. Suitable for machining flat surfaces, grooves, various formed surfaces (such as splines, gears, and threads), and special shaped surfaces of molds. According to the same or opposite direction of the main motion speed and the workpiece feed direction during milling, it is further divided into forward milling and reverse milling.
The machining accuracy of milling can generally reach IT8~IT7, and the surface roughness is 6.3~1.6 μ M.
1) The machining accuracy during rough milling is IT11~IT13, and the surface roughness is 5-20 μ M.
2) Processing accuracy IT8~IT11 during semi precision milling, surface roughness 2.5-10 μ M.
3) The machining accuracy during precision milling is IT16~IT8, and the surface roughness is 0.63~5 μ M.
CNC planing
Planer machining is a cutting method that uses a planer to perform horizontal relative linear reciprocating motion on a workpiece, mainly used for the contour machining of parts.
The machining accuracy of planing can generally reach IT9~IT7, and the surface roughness is Ra6.3~1.6 μ M.
1) The precision of rough planing can reach IT12~IT11, and the surface roughness is 25~12.5 μ M.
2) The precision of semi precision planing can reach IT10~IT9, and the surface roughness is 6.2~3.2 μ M.
3) The precision of precision planing can reach IT8~IT7, and the surface roughness is 3.2~1.6 μ M.
CNC grinding
Grinding refers to the process of using abrasives and grinding tools to remove excess material from workpieces, which is widely used in the mechanical manufacturing industry as a precision machining method.
Grinding is usually used for semi precision and precision machining, with an accuracy of IT8~IT5 or even higher. The surface roughness is generally ground to 1.25~0.16 μ M.
1) The surface roughness of precision grinding is 0.16~0.04 μ M.
2) Surface roughness of ultra precision grinding is 0.04-0.01 μ M.
3) Mirror grinding surface roughness can reach 0.01 μ Below m.
CNC drilling
Drilling is a basic method of hole processing, and drilling is often carried out on drilling machines and lathes, as well as on boring or milling machines.The machining accuracy of drilling is relatively low, usually only reaching IT10, and the surface roughness is generally 12.5~6.3 μ m. Expanding and reaming are often used for semi precision machining and finishing after drilling.
CNC boring
Boring is an inner diameter cutting process that uses a tool to expand a hole or other circular contour. Its application range generally ranges from semi rough machining to precision machining, and the tool used is usually a single edge boring tool (called a boring bar).1) The boring accuracy of steel materials can generally reach IT9~IT7, and the surface roughness is 2.5~0.16 μ M.
2) The machining accuracy of precision boring can reach IT7~IT6, and the surface roughness is 0.63~0.08 μ M.
Types of CNC machining operations
CNC machining operations can be classified based on the tasks and operating methods performed.
CNC milling
CNC milling is a common type of CNC machining operation, mainly used to cut or carve the desired shape on the workpiece. In CNC milling, the workpiece is fixed on the machine tool, and the cutting tool moves on the surface of the workpiece through the CNC control system to remove material and form the desired shape. Commonly used for manufacturing various flat, contour, and hole processing workpieces. Through reasonable programming and process settings, complex shapes and detailed surface processing requirements can be achieved. Different types of milling tools and machining strategies can be used to meet different machining needs.
CNC boring
CNC boring is a common type of CNC machining operation, mainly used to expand or adjust the size and shape of internal holes in workpieces. In CNC boring, the rotating tool moves inside the workpiece through the CNC control system, removing materials to achieve the desired hole shape and size.
Commonly used for machining holes of various sizes and shapes. Through reasonable programming and process settings, precise hole processing can be achieved, and the requirements for hole diameter, roundness, parallelism, etc. can be controlled. The selection and processing strategy of boring tools depend on the material of the workpiece and the characteristics of the hole.
CNC drilling
CNC drilling is mainly used for drilling operations on workpieces. In CNC drilling, the cutting tool rotates and advances downwards on the workpiece through the CNC control system to remove material and form the required holes.
CNC drilling has the characteristics of high efficiency and precision, and is commonly used to process holes of various sizes and shapes. Through reasonable programming and process settings, precise hole processing can be achieved, and the requirements for hole diameter, roundness, depth, etc. can be controlled. Choosing appropriate drilling tools and processing strategies is the key to achieving high-quality hole processing.
CNC turning
CNC turning is a common type of CNC machining operation, mainly used for machining cylindrical workpieces. In CNC turning, the workpiece is clamped on a rotating spindle, while the cutting tool moves on the workpiece to remove material and form the desired shape. It has the advantages of high precision, high efficiency, and good repeatability, and is commonly used for manufacturing various cylindrical parts such as shafts, threads, and holes. Through reasonable programming and process settings, complex shapes and detailed surface processing requirements can be achieved.
Fix the workpiece on the rotating spindle and use a cutting tool to remove the material to obtain the desired shape. Turning operations are usually used to machine cylindrical parts.
CNC wire cutting
CNC wire cutting, also known as electric spark wire cutting. Mainly used for cutting and processing on conductive materials through electric spark discharge.
CNC wire cutting is suitable for various conductive materials, such as metals and alloys. It can achieve high-precision and complex shape cutting without generating mechanical stress, making it suitable for processing brittle and high hardness materials. The advantage of wire cutting is that it can cut very small holes and details, and can handle various complex shaped workpieces.
By applying electric spark discharge between the workpiece and the electrode, the electrode wire is cut into the desired shape. Wire cutting is commonly used to process workpieces with complex contours.
CNC grinding
CNC grinding is mainly used for grinding and polishing the surface of workpieces to improve surface quality and accuracy. In CNC grinding, the abrasive rotates, vibrates, or moves on the surface of the workpiece through the CNC control system to remove surface materials and obtain the required smoothness and shape.
CNC grinding can be used for surface grinding and polishing of various materials, such as metals, ceramics, and plastics. It can achieve high-precision, high smoothness, and complex shape surface processing, improving the smoothness, flatness, and dimensional accuracy of workpieces. By reasonable programming and grinding parameter settings, the cutting depth, grinding speed, and surface quality during the grinding process can be controlled to meet the requirements of the workpiece.