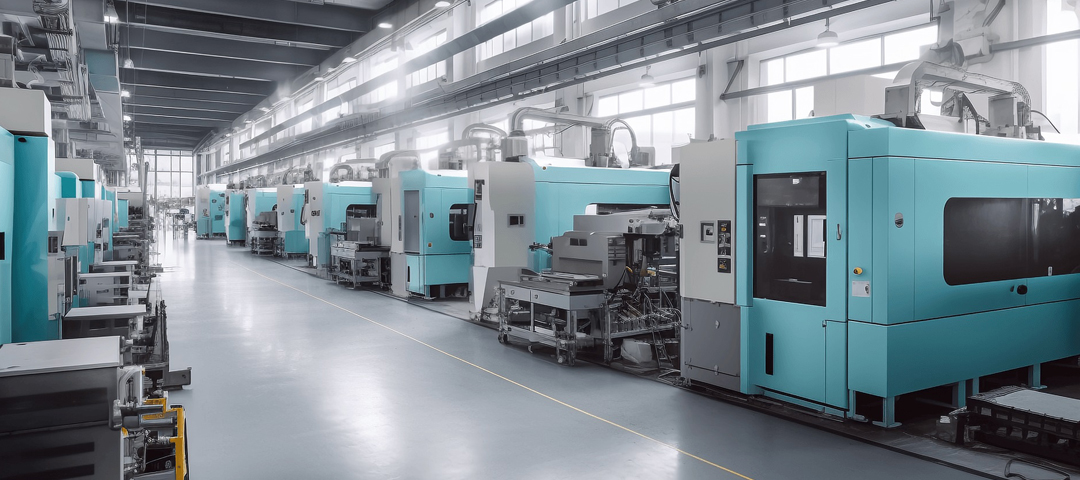
Introduction to Metal Injection Molding Process Characteristics
Metal injection molding is a high-precision manufacturing process that combines traditional plastic injection molding and powder metallurgy technology. It can be used to produce metal parts with complex shapes and high density, and is usually used to manufacture small metal parts, such as mobile phone parts, medical equipment, automotive parts, etc.
Common Materials for Metal Injection Molding
Stainless steel
Stainless steel is one of the most commonly used MIM materials, with good corrosion resistance, mechanical properties, and thermal stability. Commonly used stainless steel materials include 304, 316, and 17-4PH.
Titanium alloy
Titanium alloy has high strength, low density, and good corrosion resistance, and is widely used in fields such as aerospace and medical devices. Commonly used titanium alloy materials include Ti-6Al-4V and Ti-6Al-7Nb.
Ferroalloy
Ferroalloy has good mechanical and magnetic properties, suitable for manufacturing various industrial parts. Commonly used ferroalloy materials include low alloy steel, tool steel, and stainless iron.
Nickel alloy
Nickel alloy has excellent corrosion resistance, high-temperature strength, and thermal expansion performance, and is commonly used in fields such as aerospace, energy, and chemical engineering. Common nickel alloy materials include Inconel, Hastelloy, and Monel.
Copper alloy
Copper alloy has good conductivity, thermal conductivity, and mechanical properties, and is widely used in fields such as electronic equipment and automotive components. Common copper alloy materials include pure copper, copper zinc alloy (brass), and copper tin alloy (bronze).
The process of metal injection molding
Mix metal powder with polymer powder and additives to form an injectable paste material.Inject the mixed material into the injection machine and inject it into a specific mold through high pressure. Molds usually have the shape of the required parts.
By sintering or heat treatment, the components obtained by injection molding are spheroidized to form a metal structure.
Perform processes such as removing residual polymers, grinding, polishing, and coating to obtain the final metal parts.
Advantages of Metal Injection Molding
Complex shapes
MIM can produce complex shaped metal parts, including internal cavities, slender structures, and small holes. Compared to traditional machining methods, MIM can achieve complex shape manufacturing in one step without the need for additional machining processes.High precision
MIM can achieve high-precision metal parts manufacturing, typically with an accuracy of ± 0.3%. MIM is very suitable for applications that require precise size and shape, such as medical devices, electronic devices, etc.high density
Metal parts manufactured through MIM have high density, close to theoretical density. It has good mechanical properties, high strength, and hardness, and can meet the requirements of various applications.Mass production
MIM is suitable for large-scale production and can produce a large number of metal parts in a relatively short period of time. Compared to traditional processing methods, MIM can improve production efficiency and reduce costs.Material diversity
MIM can use various metal alloy materials, including stainless steel, titanium alloy, iron alloy, nickel alloy, etc.Design flexibility
MIM allows for complex geometric designs in the manufacturing process of parts and supports various surface treatment and post-treatment processes such as polishing, spraying, plating, etc.
Limitations of Metal Injection Molding
Part size limitations
MIM is suitable for manufacturing relatively small parts, and for larger sized parts, the cost may be higher. This is due to technical limitations in mold manufacturing, injection equipment, and spheroidization treatment.cost
Compared to traditional processing methods, MIM may have higher costs. This is due to the high cost of materials required in the MIM process, as well as the investment in complex mold manufacturing and injection equipment. However, for mass production and complex shaped parts, MIM can still reduce costs overall.Material Restrictions
Although MIM can use multiple metal alloy materials, there may be problems with component separation or poor sintering for certain special materials. In addition, some materials may not be suitable for processing through MIM, which limits the application range of MIM.Process complexity
MIM involves multiple process steps, including material preparation, injection molding, spheroidization treatment, and post-treatment. These steps require professional equipment and operation, and strict control of various parameters is required to ensure the quality of the parts. Therefore, the process complexity of MIM may pose certain challenges to the production process.long period
Compared to other manufacturing processes, the cycle time of MIM may be longer. This is due to the longer time required for injection molding, spheroidizing, and post-processing steps. Therefore, for certain applications that require rapid delivery, MIM may not be the best choice.