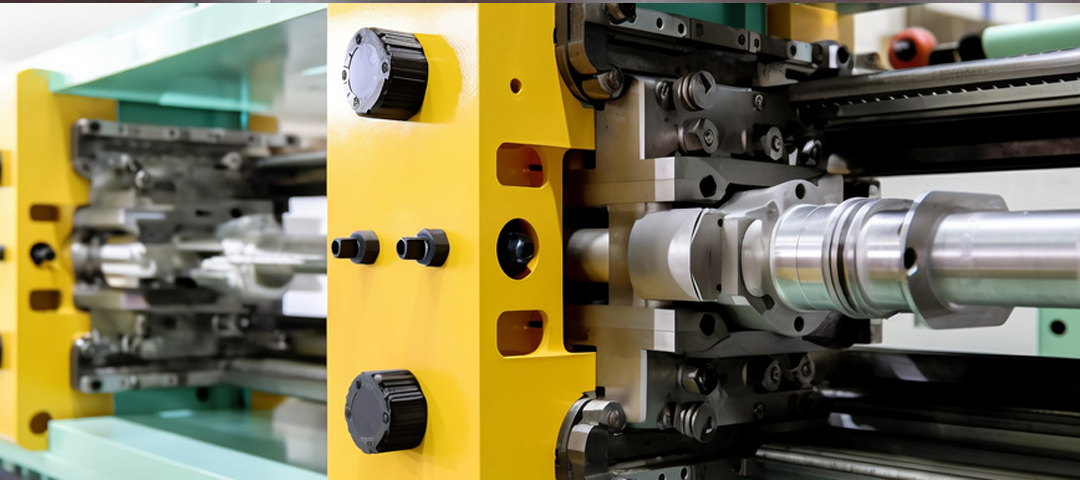
Plastic injection molding
What is plastic injection molding?
Plastic injection molding is a common plastic processing technology and a form of injection molding. The process of using an injection molding machine to inject molten plastic into a mold, and manufacturing various plastic products through cooling and solidification.
The main steps of plastic injection molding
Design and make molds: Design and make molds based on the required products. A mold usually consists of an injection mold (including the injection cavity and mold core) and an ejection mold. Injection molds are used to inject molten plastic, while ejection molds are used to eject the formed product from the mold.
Preparation of plastic materials: Select appropriate plastic materials, load plastic particles into the injection cylinder of the injection machine, and prepare for melting and injection.
Melting and injection: Plastic particles are melted into a molten state through the heater and screw in the injection cylinder. Once the preset injection conditions are reached, the injection machine injects molten plastic into the injection cavity of the mold, filling the entire cavity.
Cooling and solidification: The molten plastic in the injection cavity rapidly cools and solidifies in the mold. The length of cooling time depends on factors such as the type and thickness of the plastic. After cooling is completed, the cured plastic will maintain the desired shape.
Ejection and demolding: Once the plastic solidifies, the ejection mechanism will act on the mold, ejecting the formed product from the mold. The ejection mechanism usually consists of an ejector pin, a disc, and an ejector rod.
Cutting and sorting: After ejection, the formed product may require subsequent processing steps such as cutting, trimming, and polishing to obtain the final product form.
Plastic injection molding is an efficient, accurate, and reproducible plastic processing method. Widely used in various industries, from small components to large containers, production can be achieved through plastic injection molding. This molding technology can produce plastic products of various shapes, sizes, and complexities.
Advantages and disadvantages of plastic injection molding
Plastic injection molding has many advantages and some disadvantages.
Advantages:
High production efficiency: Injection molding is an efficient production method that can achieve large-scale and continuous production. The injection cycle is relatively short, and each cycle can produce a complete product, improving production efficiency.
High precision: Injection molding can produce high-precision and complex plastic products. The design and manufacturing accuracy of the mold determine the accuracy of the final product, which can meet various precision requirements.
Strong plasticity: Injection molding is suitable for various types of plastic materials, including thermoplastic and thermosetting plastics. Different types of plastics can meet different product requirements by adjusting injection parameters.
High degree of automation: The injection molding process can be automated, reducing the need for manual operations and improving production efficiency and consistency.
Stable product quality: Injection molding can produce consistent product quality, with each product having the same shape, size, and performance characteristics.
Disadvantages:
High initial cost: The production of injection molding molds requires a high initial investment. The design and manufacturing costs of molds are relatively high, especially for large and complex molds.
Design limitations: The design of injection molded products needs to consider mold limitations, such as wall thickness, size, shape, etc. Some complex shaped products may require special mold design and manufacturing.
Environmental impact: The waste and exhaust gas generated during the injection molding process have a certain impact on the environment, and appropriate environmental protection measures need to be taken for treatment and disposal.
Process debugging is complex: different plastic materials and product requirements may require different injection parameters and process debugging. For products that are first put into production, multiple adjustments may be required to achieve the desired production effect.
Plastic injection molding has many advantages, such as high efficiency, high precision, and strong plasticity, but there are also some drawbacks, such as high cost and design limitations. In practical applications, it is necessary to comprehensively consider these factors to determine whether to use injection molding methods.
Plastic Injection Molding Process and Machinery
Injection machine: Injection machine is the core equipment of plastic injection molding. It consists of injection system, pressure maintaining system, cooling system, lubrication system, electrical control system, etc. The main function of an injection machine is to heat and melt plastic raw materials before injecting them into the mold, and to achieve plastic shape molding through pressure and temperature control.
Mold: Mold is an important component of plastic injection molding, consisting of injection mold and ejection mold. The injection mold includes an injection cavity and a mold core, which are used to form the appearance and internal structure of the product. Ejection mold is used to eject the formed product from the mold.
Heating system: The heating system of the injection machine is mainly responsible for heating and melting plastic raw materials. Usually, electric heaters or heat pipe heaters are used to provide a heat source and heat plastic particles to a molten state.
Cooling system: After injection molding, the hot plastic needs to be quickly cooled and solidified through the cooling system. The cooling system usually uses water or oil circulation to lower the mold temperature to ensure that the product can maintain the desired shape and size.
Control System: The control system of the injection machine is responsible for monitoring and controlling the entire injection molding process. According to the set parameters, injection speed, temperature, pressure, etc. can be controlled to ensure product quality and production efficiency.
Auxiliary equipment: In the process of plastic injection molding, some auxiliary equipment is also needed, such as a feeder, dryer, cooling tower, hot runner system, etc. These equipment can be used for the supply, drying, cooling, and other processing of plastic raw materials to improve production efficiency and product quality.
Polymer in plastic injection molding
Polypropylene: Polypropylene is a common thermoplastic polymer with good chemical resistance, heat resistance, and mechanical properties. Widely used in various plastic products, such as containers, pipes, furniture, etc.
Polyethylene: Polyethylene is also a common thermoplastic polymer with good toughness and chemical stability. It can be divided into high-density polyethylene (HDPE) and low-density polyethylene (LDPE), used for manufacturing plastic bags, bottles, pipelines, etc.
Polystyrene: Polystyrene is a common thermoplastic polymer with good transparency and rigidity. Widely used in the manufacturing of packaging materials, electronic product shells, etc.
PVC: PVC is a common thermoplastic polymer with weather and chemical resistance. Widely used in building materials, wires and cables, medical equipment, etc.
Polyethylene terephthalate: Polyethylene terephthalate is a common thermoplastic polymer with good transparency and mechanical properties. Widely used in the manufacturing of plastic bottles, fibers, and food packaging materials.
In addition to thermoplastic polymers, there are also some thermosetting polymers that can be used for plastic injection molding.
Phenolic resin: Phenolic resin is a common thermosetting polymer with excellent heat resistance and electrical insulation. Widely used in the manufacturing of electrical accessories, handles, etc.
Epoxy resin: Epoxy resin is a common thermosetting polymer with excellent chemical resistance and mechanical properties. Widely used in the manufacturing of electronic components, coatings, adhesives, etc.
Reaction injection molding
Reaction Injection Molding (RIM) is a special injection molding process that differs from traditional plastic injection molding. In the RIM process, two or more liquid monomers or prepolymers are usually used to generate polymers through mixing and reaction, and then the mixture is injected into the mold for molding.
The following are the general steps of the RIM process
Material preparation: The materials used in the RIM process are usually liquid monomers or pre polymers. These materials have low viscosity and can be mixed to activate chemical reactions.
Mixing and reaction: Liquid monomers or prepolymers are mixed together in a certain proportion. The mixed material undergoes chemical reactions to form a polymer.
Injection molding: The mixed and reacted materials are injected into the preheated mold. The mold is usually a double mold (formed by two closed molds) or an open mold (formed by a single mold), depending on the shape and requirements of the product.
Filling and curing: The mixture is filled in the mold and cured within a certain period of time. The curing time and temperature depend on the characteristics of the material and product requirements.
Product demolding: After solidification, the product is removed from the mold. This usually requires a certain cooling time to ensure that the product has sufficient strength and stability.
RIM has the following characteristics and advantages
Suitable for manufacturing large, complex shapes or products with special requirements.
Multiple materials can be used, including polyurethane, epoxy resin, polyester, etc.
The forming cycle is relatively short and the production efficiency is high.
The surface of the product is smooth and does not require subsequent processing.
Material properties can be adjusted as needed, such as hardness, strength, heat resistance, etc.
Reaction injection molding is widely used in fields such as automobiles, electronics, medical devices, furniture, etc., and is particularly suitable for manufacturing products that require high strength, precision, and complex shapes.
Defects in injection molded plastics
Although injection molded plastics have broad advantages and application prospects in many applications, they may also have some drawbacks.
The following are some common defects in injection molding plastics:
Bubbles and Holes: During the injection molding process, if gas or other impurities are not completely eliminated, it may cause bubbles or holes to appear in the product. This may reduce the strength and quality of the product.
Thermal stress and deformation: The high temperature and high pressure during the injection molding process may cause thermal stress and deformation of plastic products during the cooling process. This may result in inaccurate dimensions or shape deformation.
Thermal decomposition: Some plastics are prone to thermal decomposition at high temperatures, leading to a decrease in product quality. This may lead to discoloration, odor, or reduced material performance.
Inconsistent viscosity: The viscosity of plastic materials may change during injection molding, which may lead to inconsistent fluidity. This may lead to issues such as short flow and thermal fatigue in the product.
Uneven texture: Some plastic products may experience uneven surface texture, which may be caused by problems in mold design or injection molding process. This may affect the appearance and quality of the product.
Burrs and defects: During the injection molding process, the edges of plastic products may exhibit burrs or other defects. This may require subsequent deburring or trimming processes.
Dimensional instability: Plastic may be affected by thermal and cooling shrinkage during injection molding, resulting in dimensional instability. This may require consideration of subsequent size correction or design adjustments.
These defects may affect the quality, appearance, and performance of injection molded plastic products. In order to reduce the occurrence of these defects, the injection molding process requires strict control and monitoring, and appropriate measures are taken to solve the problem.