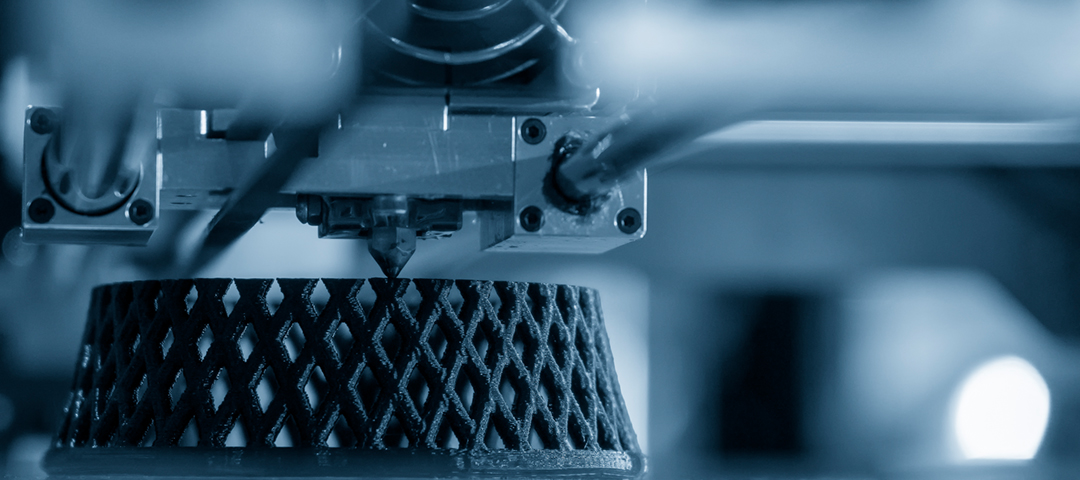
How to combine 3D printing with CNC machining?
CNC machining can further improve the accuracy, dimensional consistency, and surface quality of 3D printed parts. It can be used to process various materials, including metals, plastics, etc. The feasibility and effectiveness of CNC machining are influenced by factors such as the geometric shape, material characteristics, and processing requirements of 3D printed parts. Before conducting CNC machining, appropriate experiments and tests can be conducted to ensure the feasibility and required quality of the machining.
Method for CNC machining of 3D printed parts
Firstly, clean and cure the 3D printed parts to ensure a smooth surface and complete material curing. Remove any impurities or residues that may interfere with CNC machining.
Import CAD models of 3D printed parts into CAM software using computer-aided manufacturing (CAM) software. In CAM software, further design and preparation of parts can be carried out, including adding tool paths, setting cutting parameters, etc.
Select appropriate tools and cutting materials according to the parts and materials that require CNC machining. Select the appropriate tool type and size based on the geometric shape, material hardness, and processing requirements of the parts.
In CAM software, tool paths are generated based on the geometric shape and machining requirements of the parts. The tool path defines the trajectory of the tool movement on the part and the sequence of cutting operations.
Perform machining settings on CNC machine tools, including clamping parts, installing tools, and setting parameters such as machining speed and feed rate. Ensure the accuracy and stability of the machine tool and cutting tools.
Start the CNC machine tool and machine according to the tool path generated by CAM software. CNC machine tools will automatically control tool movement and cutting operations according to the program, gradually processing 3D printed parts into the final shape.
After completing CNC machining, subsequent treatments such as cleaning, removing cutting residues, polishing, painting, etc. are carried out to improve the surface quality and appearance of the parts.
Advantages of using CNC machine tools on 3D printed parts
Improve accuracy
CNC machine tools can provide high-precision machining capabilities, enabling more precise dimensions and shapes on 3D parts. Compared to traditional manual or semi-automatic machining methods, CNC machine tools can achieve higher accuracy in a shorter time.Automated processing
CNC machine tools are automated processing equipment that can automatically control the movement of cutting tools and the machining process through pre programmed instructions. Therefore, CNC machine tools can improve production efficiency and consistency, reduce human errors and labor costs.Complex shape processing
3D printed parts typically have complex geometric shapes, and traditional machining methods may be difficult to achieve. Using CNC machine tools, complex shapes can be machined through pre programmed tool paths, including internal holes, curve contours, etc.Multi material processing
CNC machine tools can be used to process various materials, including metal, plastic, wood, etc. This means that different materials can be used for CNC machining on 3D parts to meet specific needs and functional requirements.Surface quality improvement
3D printed parts typically have rough surfaces, while CNC machining can improve surface quality through cutting operations. By using appropriate cutting tools and cutting parameters, a smoother and more uniform surface can be achieved, improving the appearance and functionality of the parts.
Precautions when using 3D printing and CNC machining
Material selection
Choose materials suitable for 3D printing and CNC machining. Different materials have different characteristics and mechanical properties, and suitable materials need to be selected based on specific application needs.Design considerations
When designing 3D printed parts, it is necessary to consider the feasibility and limitations of processing. Avoid overly complex or impossible geometric shapes to ensure the machining feasibility and stability of the parts.Supporting structure
For 3D printed parts, it may be necessary to add support structures to support suspended parts and complex geometric shapes. When designing, consideration should be given to the addition of supporting structures and subsequent removal processes.Processing parameters
When conducting CNC machining, it is necessary to set appropriate machining parameters based on the characteristics of materials and parts, including cutting speed, feed rate, cutting depth, etc. Adjusting these parameters can affect the machining effect and part quality.Positioning and clamping
Ensure stable positioning and clamping of 3D printed parts during the machining process. Use appropriate fixtures and positioning methods to avoid movement or deformation of parts during the machining process.surface treatment
Perform surface treatment on 3D printed parts as needed, such as polishing, spraying, etc., to improve surface quality and appearance.quality control
Quality control and inspection are carried out during the manufacturing process to ensure that the dimensions, shape, and surface quality of the parts meet the requirements. Measurement tools and testing equipment can be used for inspection.Safe operation
When conducting 3D printing and CNC machining, it is necessary to comply with safety operating procedures, wear personal protective equipment, and avoid accidental injury and equipment damage.