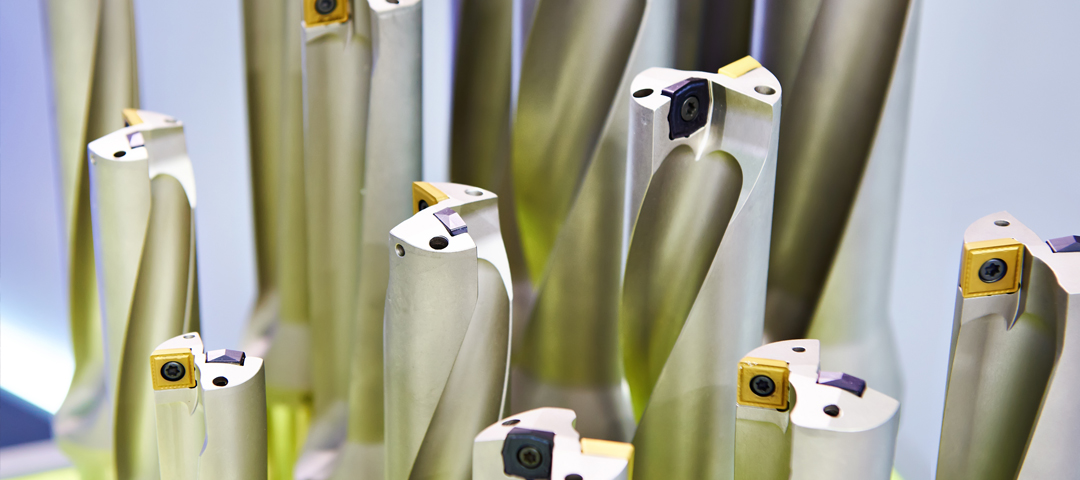
The Important Influence of CNC Cutting Tools on CNC Machining
Choosing the correct CNC tool is the key to ensuring the quality of CNC machining, improving production efficiency, extending tool life, ensuring safety, and controlling costs. Before selecting a tool, it is necessary to fully understand the processing requirements, material characteristics, and cutting parameters, and refer to professional advice or consult tool suppliers to ensure that the most suitable tool is selected to meet your processing needs.
Select the tool material according to the type and characteristics of the processing material. For example, for cutting hard materials such as steel or iron, high-speed steel (HSS) or hard alloy (carbide tool) can be chosen. For difficult to cut materials such as superalloys, Superhard material such as cubic Boron nitride (CBN) or polycrystalline diamond (PCD) can be selected.
Select the appropriate tool type according to the needs of the machining operation. Common CNC tools include end mills, ball end mills, drilling cutters, turning tools, etc. Select the appropriate tool type based on the shape and processing requirements of the parts.
The geometric characteristics of the cutting tool have a significant impact on the machining effect and cutting force. For example, parameters such as the angle, length, and number of cutting edges of a tool can affect cutting force, cutting speed, and surface quality. Select appropriate tool geometry parameters to meet machining requirements and improve production efficiency.
Select appropriate cutting parameters based on factors such as the hardness of the processed material, cutting depth, and feed speed. This includes cutting speed, feed rate, cutting depth, and cutting rate. Ensure that the cutting tools match the cutting parameters to improve cutting efficiency and extend tool life.
Consider selecting coated tools. Coatings can provide better wear resistance, high-temperature stability, and lubricity, thereby extending tool life and improving surface quality during machining. Common tool coatings include Titanium carbide coating, Titanium carbide nitrogen coating and diamond coating.
Choose well-known brands and high-quality tool suppliers. High quality cutting tools typically have better cutting performance, wear resistance, and stability, providing better machining results and longer service life.
Comprehensively consider the price, performance, and lifespan of cutting tools to determine the best cost-effectiveness. A higher initial investment may result in longer tool life and better machining results, but it needs to be evaluated based on specific circumstances.
The most important thing is to fully understand the machining requirements, material characteristics, and cutting parameters before selecting CNC tools, and refer to professional advice or consult tool suppliers to ensure the selection of the most suitable tool to meet your CNC machining needs.
Selection of CNC machining tools
CNC cutting tools are specialized tools used for automated cutting processing on CNC machine tools. Adopting advanced design and manufacturing technology, aiming to improve processing efficiency, quality, and accuracy.
CNC cutting tools include various types such as milling cutters, drill bits, turning tools, thread cutters, boring cutters, etc. Each type of tool has its specific purpose and applicability. For example, milling cutters are used for flat milling, three-dimensional milling, and contour machining; Drill bits are used for hole processing; Turning tools are used for turning operations, etc.
NC tools are usually made of high-speed steel, hard alloy, ceramic materials, polycrystalline cubic Boron nitride, polycrystalline diamond and other materials. Different materials have different hardness, wear resistance, and thermal stability to adapt to different processing materials and requirements.
The geometric features of CNC cutting tools include blade angle, blade length, number of blades, blade shape, and shank shape. These characteristics determine cutting force, cutting efficiency, and machining quality. The selection of tool geometry depends on the processing material, processing method, and accuracy requirements.
CNC tools are often coated with special coatings to improve tool performance. Common coatings include Titanium carbide, titanium nitride, aluminum nitride, aluminum oxide, etc. These coatings can provide better wear resistance, thermal stability, and lubricity, extend tool life, and improve surface quality during machining.
CNC cutting tools can be fixed by clamping, directly installed, or connected to the machine tool through a tool handle. Clamping and fixing usually use fixtures, tool handles, and fixture bolts to ensure the stability and accuracy of the tool.
The cutting parameters of CNC tools include cutting speed, feed rate, cutting depth, and cutting rate. These parameters should be reasonably selected based on the processing material, tool type, and processing requirements to achieve the best processing effect.
For CNC tools, tool management is very important. It includes tool selection, tool life monitoring, tool replacement and maintenance, etc. Reasonable tool management can improve production efficiency, reduce costs, and ensure machining quality.
CNC cutting tools play an important role in modern manufacturing. Understanding different types of tools, tool materials, geometric features, and cutting parameters, as well as the importance of tool management, can help you choose suitable CNC tools and achieve efficient, accurate, and stable quality cutting processing.
Evaluation Techniques for CNC Machining
Determine the specific type of machining you need to perform, such as milling, drilling, turning, threading, etc. Understanding the type of machining required can help you choose the appropriate CNC machine tool and cutting tool.
Determine the type of material you need to process, such as metal, plastic, wood, etc. Different materials may require different types of CNC machines and tools, as the cutting characteristics and processing requirements of different materials vary.
Determine the size range and required accuracy level of the parts you need to process. This will help you choose the appropriate CNC machine tool and cutting tool, as well as determine the required cutting parameters and processes.
Determine your processing batch, which is the number of parts required for each processing. If you need large-scale production, you may need to consider CNC machine tools with higher efficiency and automation.
Evaluate the complexity of your processing task. If complex contour machining, surface machining or Multiaxis machining are required, you may need to consider multi axis CNC machine tools and corresponding tools.
Determine your requirements for processing efficiency. If you need fast machining and high production efficiency, you may need to choose high-speed CNC machine tools and tools with high cutting speeds.
Based on your budget constraints, evaluate the types of CNC machine tools and cutting tools you can invest in. Different types of CNC machine tools and cutting tools have different prices, and you need to make reasonable choices based on the actual situation.
Taking into account the above factors, you can better evaluate your CNC machining needs and choose suitable CNC machine tools and cutting tools to meet your machining requirements. If you are unsure or have specific machining needs, it is recommended to consult a professional CNC machining service provider or machine tool manufacturer for more detailed advice and technical support.