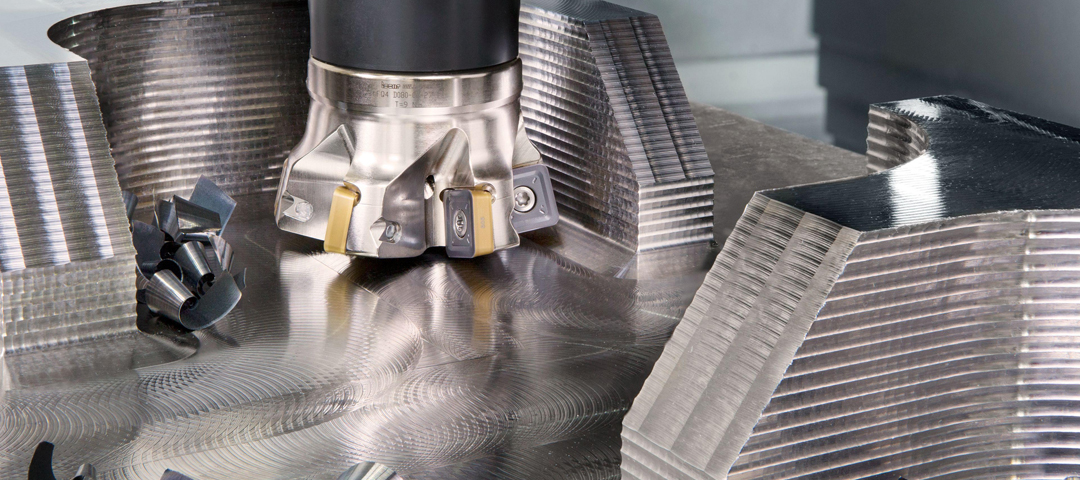
What is insert injection molding?
What is insert injection molding?
Insert injection molding is an injection molding technique used to embed two or more parts or components of different materials into injection molded parts during the injection molding process. This technology can achieve the combination of multiple materials in a single process, providing higher functionality and design flexibility.
The process of injection molding for embedded parts
Insert preparation: Different materials of inserts or components need to be prepared in advance and ensure that their size and shape are suitable for injection molding.
Mold design
Design appropriate injection molds based on the requirements of injection molded parts and inserts. Molds typically have specific structures or cavities for accommodating and locating inserts.
Injection molding process
In an injection molding machine, a material (usually melted plastic) is first injected into a part of the mold to form a part of the part. Then, the insert is placed in the mold and further injected with another material to surround and secure the insert. Finally, after the plastic has cooled and solidified, the mold is opened to complete the molding of the injection molded parts.
Embedded injection molding technology can be used for various applications, such as embedding circuit boards, sensors or connectors in electronic products, embedding metal components in automotive parts, and embedding pipelines or valves in medical devices. It can provide higher assembly efficiency and product integration, reduce production steps and lower costs.
What is the inlay molding process?
Insert molding process is a process of simultaneously molding inserts or components with injection molded parts. Integrating inserts or components into injection molded parts during the injection molding process. The embedded molding process is commonly used in manufacturing processes such as injection molding, die casting, and extrusion.
The steps of the inlay forming process
Material preparation: Prepare injection molding materials and insert materials, and ensure compliance with design requirements. Injection molding materials are usually melted plastic, while insert materials can be metal, plastic, rubber, or other materials.
Mold design
Design suitable molds to accommodate and position inserts, and ensure that the shape and size of the injection molded parts meet the requirements. The design of the mold needs to consider the shape, size, position, and fixing method of the inserts.
Injection molding process
Heat and melt the injection molding material, and then inject it into the mold through an injection molding machine. During the injection molding process, place the insert in the mold and ensure its correct position. As the injection molding material is injected, it will surround and fix the insert.
Cooling and Curing
After the injection molding material cools and solidifies, open the mold and take out the molded injection molding parts. At this point, the embedded parts have been integrated with the injection molded parts, forming a complete finished product.
The embedded molding process can provide higher assembly efficiency and product integration, reduce production steps and lower costs. Widely used in industries such as automobiles, electronics, and medical devices, for manufacturing parts and components with complex structures and functions.
What are the advantages of embedded molding?
Insert molding has many advantages, making it a popular manufacturing process.
Integrated design
Insert molding can simultaneously shape inserts or components with injection molded parts, achieving integrated design. This can reduce assembly steps and the number of parts, simplify product structure, and improve assembly efficiency.
Cost effectiveness
Insert molding can reduce production steps, improve production efficiency and product consistency, thereby reducing production costs. Meanwhile, integrated design can reduce component procurement and inventory costs.
Structural strength
Insert molding can firmly embed inserts into injection molded parts, providing better structural strength and stability. This integrated design can reduce looseness or mismatch between parts, improve product reliability and durability.
Multi material combination
Insert molding can achieve the combination of different materials to meet the specific requirements of the product. By selecting appropriate injection molding materials and insert materials, different physical and chemical properties can be achieved, such as hardness, strength, conductivity, corrosion resistance, etc.
Design flexibility
Embedded molding can fully consider the position, size, and fixing method of the embedded parts during the design phase, thereby providing greater design flexibility. Designers can choose appropriate inserts and injection molding materials based on product requirements to achieve more complex structures and functions.
Space saving
Insert molding can merge multiple parts or components into one unit, reducing the size and space requirements of the product. This is very beneficial for compact products and limited space applications.
Embedded molding provides an efficient, economical, and flexible manufacturing process that can meet the manufacturing needs of complex parts and components. Bringing many advantages to product design and production, thereby improving product quality, reliability, and competitiveness.
Are there any special precautions for the molding of inserts?
There are several special considerations when forming inserts.
Insert selection
It is very important to choose the insert material that is suitable for the molding of the insert. The embedded material should have good heat resistance, chemical resistance, and mechanical strength to withstand high temperatures and pressure during the injection molding process.
Mold design
The design of the mold needs to consider the shape, size, position, and fixing method of the inserts. Ensure that the mold can correctly accommodate and position the insert, and ensure that the injection molding material can fully surround and secure the insert.
Injection molding parameter adjustment
Due to the presence of inserts, the injection molding parameters during the injection molding process may need to be adjusted. For example, injection temperature, injection pressure, and injection speed may need to be optimized to ensure that the injection material fully covers and secures the insert, while avoiding excessive heating or damage to the insert.
Mold cooling
As the injection molding material needs to be heated during the molding of the insert, the cooling of the mold is also very important. Appropriate cooling design can ensure rapid cooling and solidification of injection molded materials, thereby improving production efficiency and product quality.
Placement and fixation of inserts
It is also crucial to correctly place and secure inserts in the mold. The insert should maintain a stable position during the injection molding process to avoid movement or deformation. Appropriate fixing methods, such as using locating pins or fixtures, can ensure accurate positioning of the insert.
Compatibility between insert and injection molding materials
Ensure compatibility between insert and injection molding materials, and avoid possible chemical reactions or degradation. When selecting insert materials, compatibility and adhesion with injection molding materials need to be considered.
Special attention should be paid to the selection of inserts, mold design, injection molding parameter adjustment, mold cooling, insert position and fixation, as well as the compatibility between inserts and injection molding materials in the process of insert molding. The reasonable application of these precautions will help ensure the success of embedded component molding and the improvement of product quality.