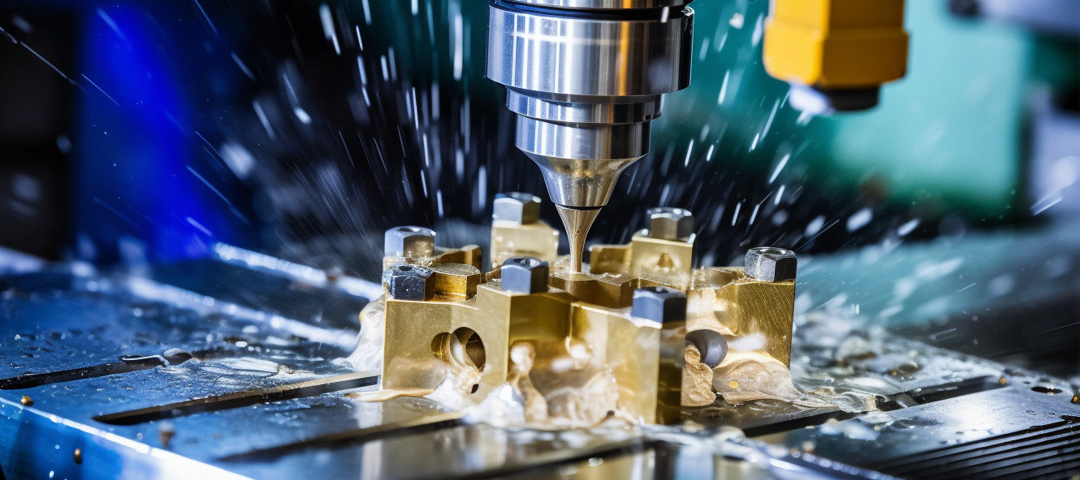
What is CNC Milling Machining ?
CNC milling machining is an automated machining method controlled by computers, used to manufacture various components and workpieces. Use a CNC milling machine for processing, milling off the material on the surface of the workpiece to obtain the desired shape and size.
During the CNC milling process, computer programs guide the movement and operation of milling machines. The program includes geometric data and machining paths of the workpiece, as well as relevant parameters of the tool. By inputting this information into the CNC milling machine control system, the machine can automatically execute operations according to the program, achieving high-precision and high-efficiency machining.
CNC milling machining is used to process various materials, such as metals, plastics, and composite materials. Produce various shapes of workpieces, including flat surfaces, curved surfaces, holes, and threads. Compared to traditional manual or semi-automatic machining methods, CNC milling has higher accuracy, repeatability, and production efficiency.
CNC milling machining processing method
Firstly, it is necessary to use computer-aided design software (CAD) for design based on the design requirements of the required parts. Determine the geometric shape, dimensions, and processing requirements of the parts.
Based on the designed parts, use computer-aided manufacturing software (CAM) to write machining programs. This program describes the tool path, cutting parameters, and process requirements of the machine tool during the milling process.
Fix the workpiece on the workbench of the CNC milling machine and use fixtures to ensure the stability and accuracy of the workpiece during the machining process.
Select the appropriate tool according to the requirements of the machining program and fix it on the spindle of the CNC milling machine. Ensure that the distance and angle between the cutting edge of the tool and the surface of the workpiece are correct.
According to the requirements of the machining program, set the machining parameters of the CNC milling machine, such as cutting speed, feed speed, cutting depth, and cutting direction. These parameters will affect the cutting effect and surface quality of the workpiece during the machining process.
Load the machining program into the control system of the CNC milling machine and start the machining process. The CNC milling machine will perform cutting operations according to the path and parameters set in the program, gradually removing the surface of the workpiece to obtain the desired shape and size.
Types of CNC milling processing
Flat milling (2.5D milling)
Plane milling is one of the most basic types of CNC milling processing. It removes materials by moving the milling tool on the workpiece plane to achieve machining of the workpiece plane.
3D milling
Stereo milling is the addition of complex shapes such as tilting, curves, and surfaces to the machining of flat milling. It can achieve three-dimensional machining of workpieces through multiple tool paths and cutting directions.
High speed milling
High speed milling refers to the milling process carried out with high-speed rotating tools and rapid feed rates. It can improve processing efficiency, reduce processing costs, and achieve better surface quality.
Spiral milling
Spiral milling is a special type of machining that involves milling according to the shape of the helix through the rotation and feed motion of the cutting tool. It is commonly used for manufacturing threaded holes, threaded shafts, and other workpieces.
Engraving and milling
Engraving and milling is a processing method used to manufacture detailed carvings, patterns, and text. It can perform complex carving and sculpture on the surface of the workpiece according to design requirements.
profile milling
Profile milling is a milling process that follows a predetermined contour path. It is suitable for manufacturing workpieces with complex contour shapes, such as curves, surfaces, and unconventional shapes.
Deep hole milling
Deep hole milling is a processing method used to manufacture deep holes. By extending the length of the cutting tool and selecting appropriate cutting parameters, deep hole milling can be achieved.According to specific part design and processing requirements, appropriate CNC milling processing types can be selected. CNC milling has the advantages of high precision, high efficiency, and flexibility, and is widely used in various industrial fields.
Application of CNC milling processing
Automobile manufacturing
CNC milling is used in the manufacturing of automotive components, such as engine parts, chassis components, body structures, etc. Realize high-precision machining to ensure the quality of parts and the accuracy of mutual matching.
Aerospace
The aerospace industry has very high requirements for the accuracy and materials of components. CNC milling can be used to manufacture aircraft engine components, aerospace structural components, aerospace electronic components, etc.
Electronic manufacturing
Precision parts and shells in electronic products typically require CNC milling to achieve high-precision and complex shapes. For example, the shells, heat sinks, etc. of mobile phones, computers, and electronic devices.
Medical equipment
Medical equipment requires high precision and reliability. CNC milling is used to manufacture medical devices and components such as artificial joints, implants, and surgical instruments.
Mold manufacturing
CNC milling processing can be used for the manufacturing of molds, such as injection molds, die-casting molds, stamping molds, etc. Capable of achieving complex shapes and high-precision mold processing.
General Machinery Manufacturing
CNC milling processing is applied in the field of general machinery manufacturing, such as tool manufacturing, bearing manufacturing, machine tool manufacturing, textile machinery, etc. Capable of efficiently processing components of various shapes and sizes.CNC milling processing is widely used in the manufacturing industry, which can meet the machining needs of high precision, high efficiency, and complex shapes. Improved production efficiency, reduced costs, and provided better product quality and competitiveness for manufacturers in various fields.
Common problems in CNC milling processing
Analysis of the causes of tool wear?
Due to the contact between the tool and the surface of the workpiece during the machining process, the tool will be subject to wear and tear. Tool wear can lead to a decrease in machining quality and deviation in workpiece size. Regular inspection and tool replacement are the key to solving this problem.
What to do if the cutting overheats?
During high-speed milling and mass cutting, the cutting area may overheat, leading to an increase in surface roughness and a decrease in workpiece quality. The use of appropriate cutting lubrication and coolant can solve this problem.
Why is the deformation of the part? How to solve it?
Some materials may undergo thermal or mechanical deformation during processing, resulting in deviations in the size and shape of the workpiece. Reasonable clamping and stable processing conditions can reduce part deformation.
How to handle program errors?
Errors or inaccurate inputs in the program may lead to machining deviations or workpiece damage. Careful inspection and verification of the program to ensure accuracy is the key to avoiding this issue.
What are the reasons for vibrations and vibrations during the processing?
Under high-speed milling and unstable cutting conditions, machine tools and workpieces may experience vibrations and vibrations, leading to a decrease in machining quality and uneven surface of the workpiece. Proper cutting parameters and maintenance of machine tool stability can reduce this issue.
How can CNC milling save costs?
The processing of complex shapes may require longer processing time and more tool operations, increasing processing costs. Optimizing machining paths, improving cutting efficiency, and reasonable tool selection can reduce machining time and costs.