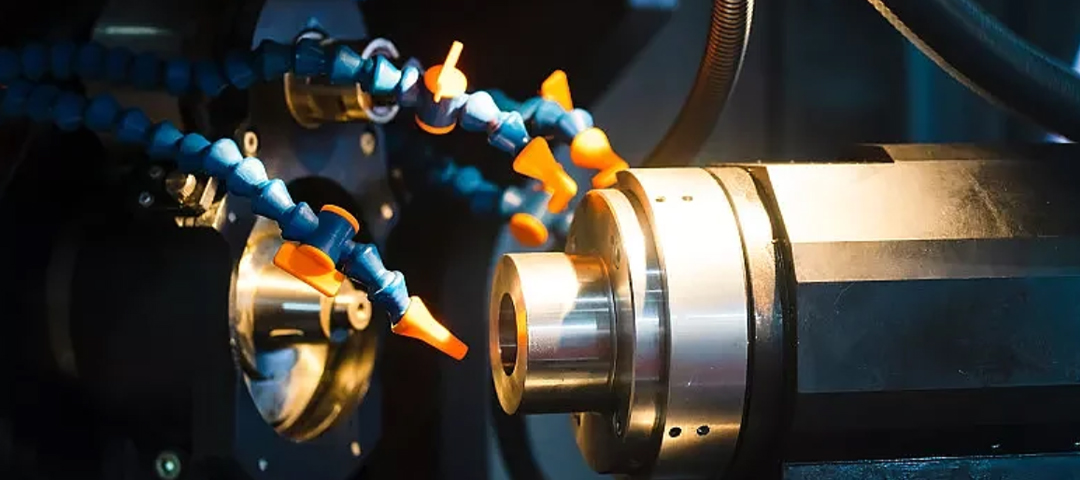
CNC machining customization for small batch parts using CNC lathes
What is CNC machining?
CNC machining is a method of automated machining of mechanical equipment using computer control systems. It controls machine tools and tools through pre programmed instructions to perform precise cutting, drilling, milling, turning, and other processes to produce complex parts and products.The basic principle of CNC machining is to convert the designed part model or process diagram into computer recognizable instruction codes, and then transmit these instructions to the CNC machine tool through the computer control system. CNC machine tools automatically control parameters such as tool movement, speed, and cutting depth based on instruction codes for precise machining.
Advantages of CNC machining
High precision
CNC machine tools can achieve highly precise machining and control the size and shape of workpieces within the micrometer level.high efficiency
CNC machining can automate the execution of machining processes, reduce manual intervention and operation time, and improve production efficiency.flexibility
By changing the instruction code, CNC machine tools can process parts of different shapes and sizes, with strong adaptability and flexibility.Good repeatability
CNC machining can achieve precise repetitive processing, ensuring that the quality and size of each part are consistent.Programmability
By writing and modifying instruction code, rapid development and production of new products can be achieved.Automation control
CNC machine tools have functions such as automatic tool replacement, automatic machining parameter adjustment, and automatic measurement, reducing the workload and error rate of operators.
How does CNC machining work?
CNC machining is the process of automated machining of mechanical equipment through a computer control system.Step 1: Design parts
First, use Computer-aided design software to create or import 3D models of parts. This model describes the geometric shape, dimensions, and features of the parts.Step 2: Create a machining program
Next, use the Computer-aided manufacturing software to convert the part model into the instruction code that can be recognized by the machine tool. This process is called post-processing, which takes into account the characteristics of the machine tool and the requirements of the machining process to generate instructions suitable for the machine tool control system.Step 3: Load the program
Load the generated instruction code into the control system of the CNC machine tool. This is usually done through transmission media (such as USB, Ethernet) or directly connected to a computer on the machine tool.Step 4: Set up workpieces and tools
Install the workpiece to be processed onto the machine tool and select the appropriate tool. Machine tools are usually equipped with an automatic tool replacement system, which can automatically select and replace tools according to the requirements of the processing program.Step 5: Run the machining program
Start the machining program through the control system and control the action of the machine tool according to the instruction code. The control system controls the movement, speed, and cutting depth of tools through motors and transmission devices, achieving precise machining.Step 6: Monitoring and Adjusting
During the machining process, the control system can monitor the machining process in real-time through sensors and measuring equipment. If necessary, adjustments can be made based on the monitoring results to ensure the accuracy of processing quality and dimensions.Step 7: Complete machining
Once the machining is completed, the machine tool will stop working and remind the operator to proceed with the next steps, such as switching workpieces or checking the quality of the parts.The key to CNC machining is the computer control system, which automatically controls the motion and cutting parameters of the machine tool based on pre programmed instruction codes, achieving precise and efficient machining processes. This automated processing method provides higher accuracy, efficiency, and consistency, suitable for producing various complex parts and products.
What are the different types of CNC machining processes?
CNC drilling
Using a rotating tool to drill holes into the workpiece is commonly used to create holes and locate holes.CNC milling
By rotating the tool to perform lateral or end cutting on the workpiece, it is used to create shapes such as planes, grooves, and contours.CNC turning
Fix the workpiece on the rotating spindle, and then use a tool to cut the outer diameter and inner diameter of the rotating workpiece for machining cylindrical parts.CNC boring
Use a special boring cutter to expand the diameter of the hole and perform precision machining, for processing precision holes.CNC discharge machining
Peel off the metal on the surface of the workpiece through electric discharge, used for processing hard materials or complex shaped parts.CNC wire cutting
Cutting wires into desired shapes through electric spark discharge is used for machining thin materials, complex contours, and internal and external shapes.CNC laser cutting
Using a high-energy laser beam to cut the workpiece material into the desired shape, commonly used for processing materials such as metal, plastic, and wood.CNC welding
Use laser welding or arc welding and other methods to connect different parts of parts or materials together.CNC grinding and polishing
Use grinding wheels or grinding tools to grind and polish the surface of the workpiece to improve surface quality and accuracy.What materials can be used for CNC machining?
metallic material
CNC machine tools are suitable for processing various metal materials, such as steel, iron, aluminum, copper, titanium, nickel alloys, stainless steel, etc. These materials are commonly used in the manufacturing of automotive parts, aerospace components, industrial equipment, etc.Plastic materials
CNC machine tools can process various plastic materials, such as polyethylene (PE), polypropylene (PP), polyvinyl chloride (PVC), polystyrene (PS), polycarbonate (PC), etc. These materials are commonly used in the manufacturing of plastic parts, electronic product casings, pipelines, and containers.Wood materials
CNC machine tools can process various wood materials, such as solid wood, plywood, fiberboard, etc. These materials are commonly used in the manufacturing of furniture, wooden crafts, building structures, etc.composite material
CNC machine tools can process various composite materials, such as carbon fiber composite materials, glass fiber composite materials, etc. These materials have the characteristics of high strength and lightweight, and are commonly used in fields such as aerospace, automobiles, and sports equipment.